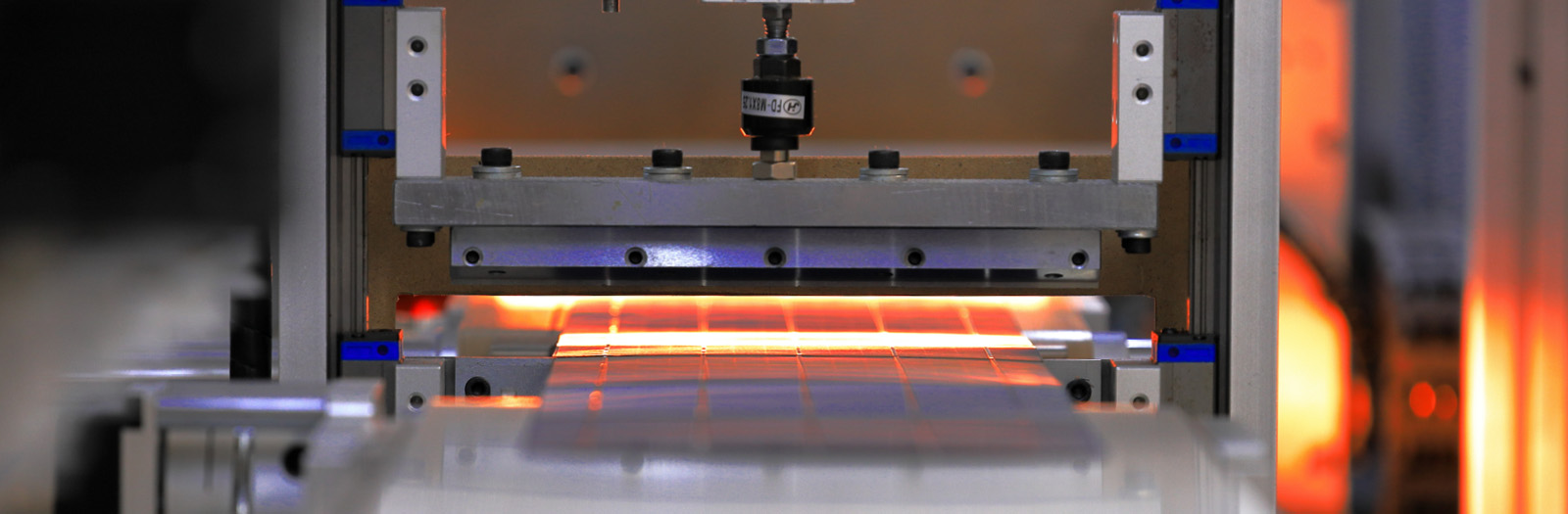
Si-Factory
Si-Factory is a project carried out by Roltec in parallel with a thin-layer photovoltaic design. We launched the production of high -quality monocrystalline silicon modules . Intensive expansion: the new hall and production line already in 2024 allowed for significant automation and ankle production increase. We combine production with the direct implementation of photovoltaic farms.
The project financed and implemented entirely from the company's funds is mainly used to meet its own energy needs. The entire production is directed directly to the implementation of our installations. We have developed and implemented a complete solar farm system for all types of surfaces. We install our modules with the help of third -party companies on flat, oblique roofs and on the ground. We estimate installations planned in the coming years at 40 MW. In 2024, we implement investments in the Greater Poland, Łódź and Lower Silesian Voivodships with a total power of nearly 10 MW.
Full Bifacial Module G1
Roltec Bifacial G1 modules have glass on both sides, unlike traditional modules. The active layer is on two sides, so light is absorbed from both sides (i.e. also the light reflected from the substrate). The modules achieve efficiency at the peak point that is up to 30% higher compared to single-sided PV modules (which depends mainly on the albedo of the substrate). Additionally, glass-glass technology increases the module's lifespan. It is highly resistant to mechanical damage, microcracks, salt mist, ammonia and fire.
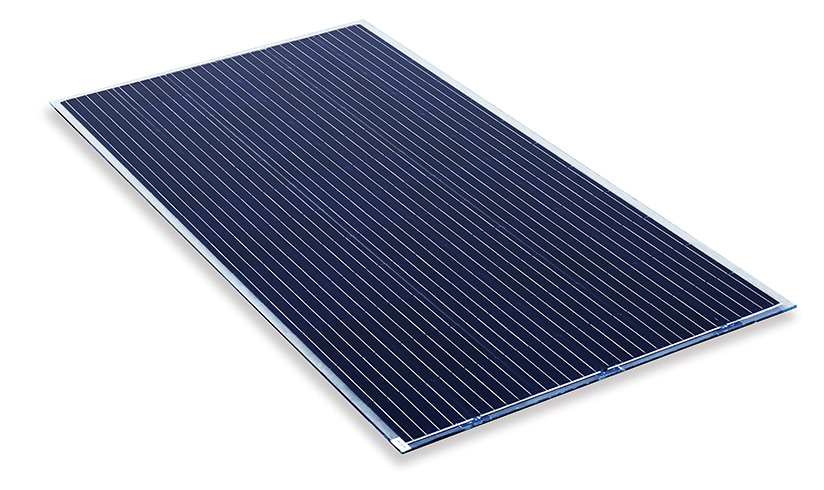
Module type: BIG1CC72-PPYYWW-NN
- Power: 395 - 405 Wp
- Size: 1920x1020 mm
- Maximum efficiency: 21.5%
- Low operating temperature
- High mechanical resistance
Production technology
Monocrystalline silicon photovoltaic modules are made on a partially automated production line, guaranteeing high quality and repeatability of the process. At the same time, our research and development department is constantly working to improve the efficiency, quality and durability of our modules.
The first stage of producing photovoltaic modules is connecting individual cells in series using connecting tapes. During the soldering process, the employee eliminates damaged cells. The connected cells are placed on glass covered with EVA foil and then electrically connected (soldered) to each other. After connection, subsequent layers of EVA foil and 3 mm tempered top glass are applied, protecting the module against external factors. Then the edges of the module are secured with a special tape. The module prepared in this way is laminated (in an oven) at a temperature of approximately 140°C, where it is completely poured. In the final stage, a junction box with cables is mounted to the bottom surface of the module.
Ready photovoltaic modules are checked on a solar radiation simulator under standard test conditions (STC: 1000 W/m2, 25°C, AM1.5G), where electrical parameters are determined, such as maximum power (Wp), short-circuit current (Isc), open circuit voltage (Voc). The modules meet all applicable standards for the design and safety of photovoltaic modules (IEC61215, IEC61730, IEC63092, IEC TS 62941).
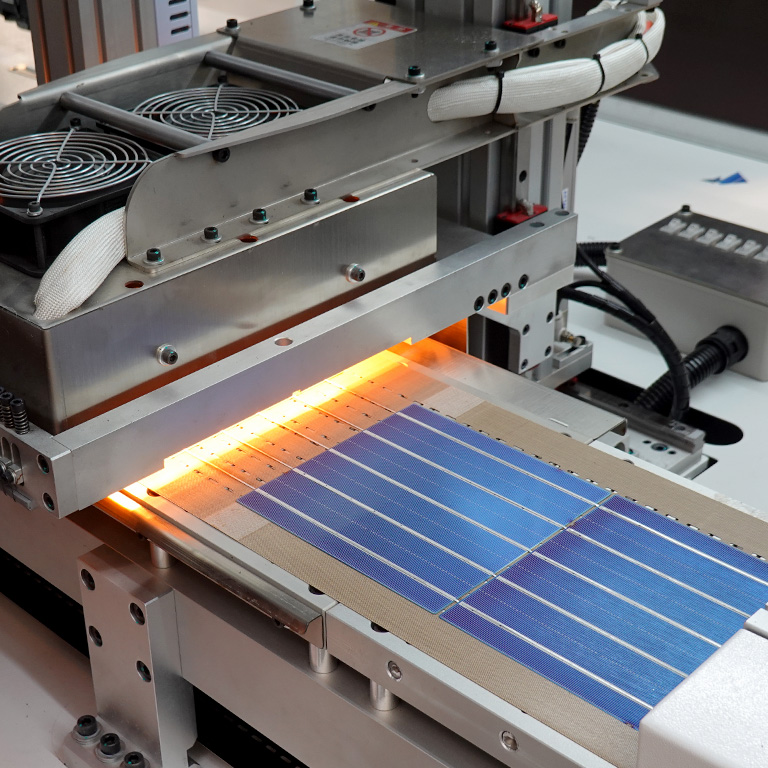
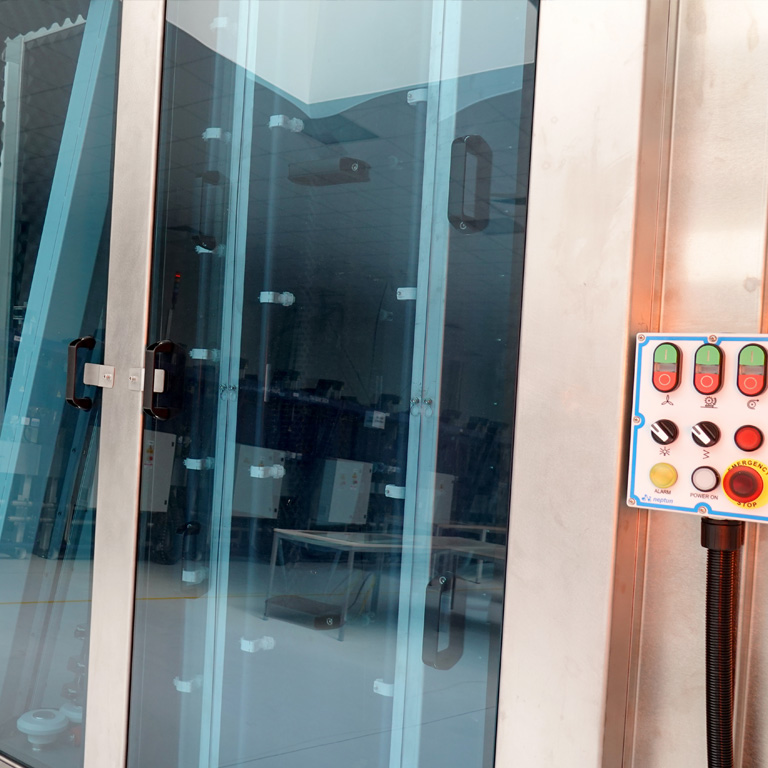
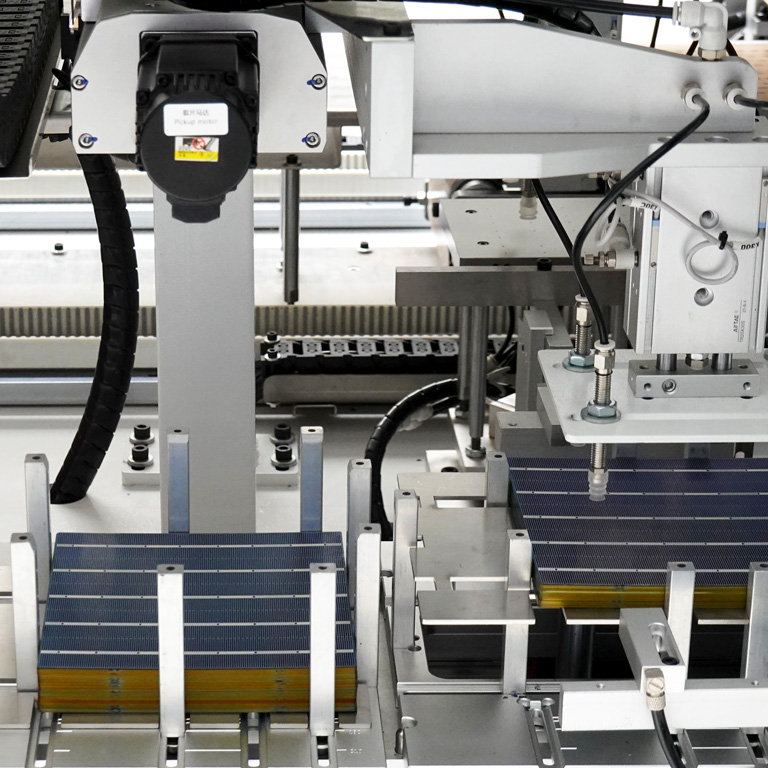
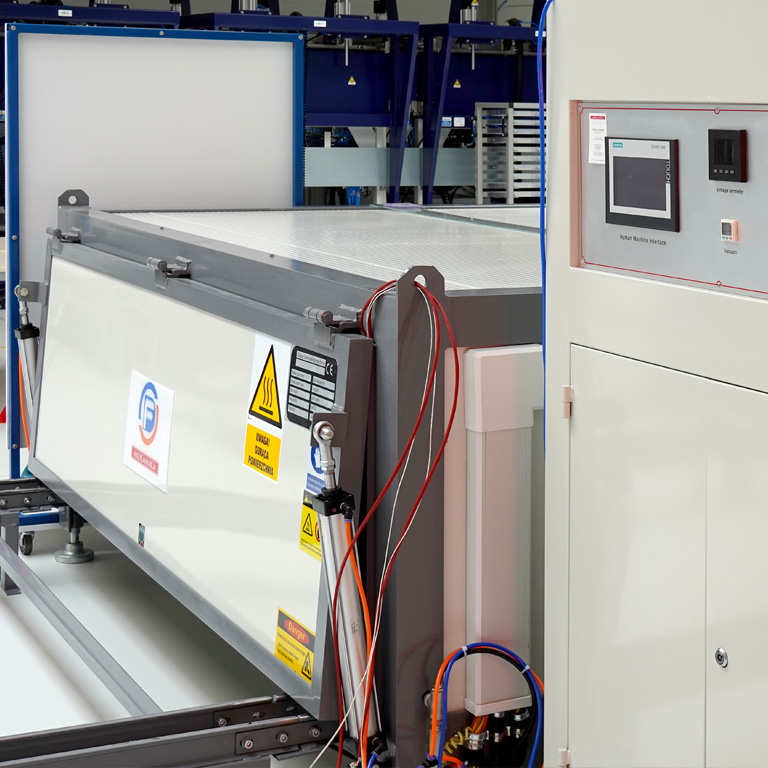
Si-Factory in numbers:
Our projects
We implement photovoltaic installations on roofs and on the ground based on dedicated and proven components.
A comprehensive approach - from the production of modules to the construction of the farm guarantees maximum reduction in kWh production costs. Complete installation includes:
- G1 solar modules,
- supporting structure,
- inverters (Sofar),
- wiring,
- electricity meters,
- monitoring application.
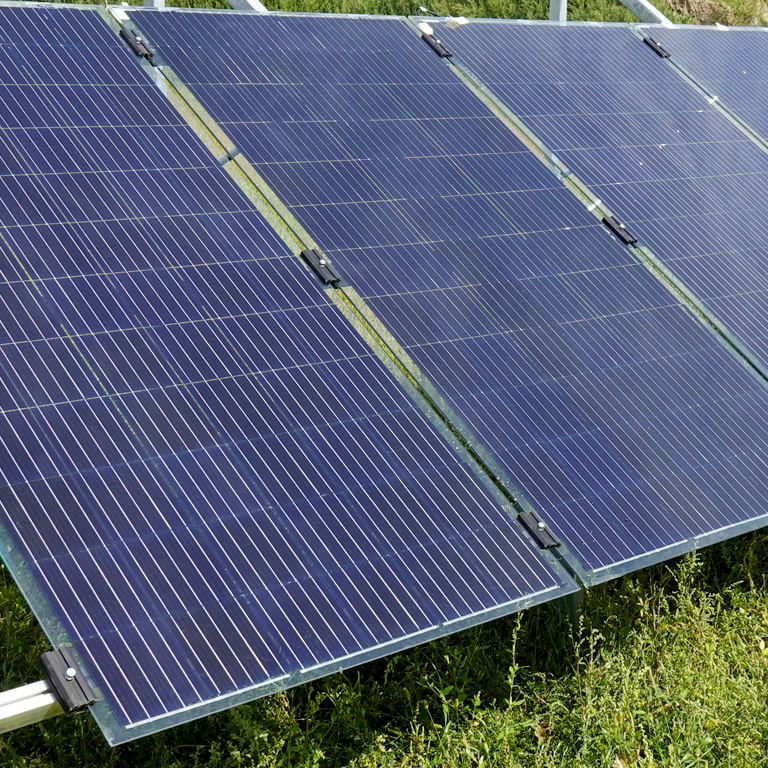
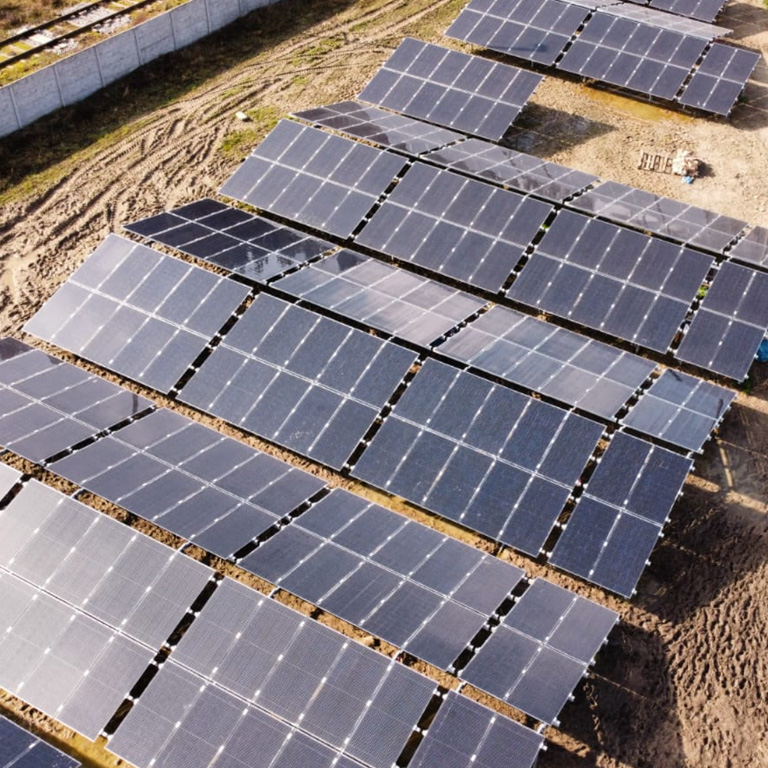
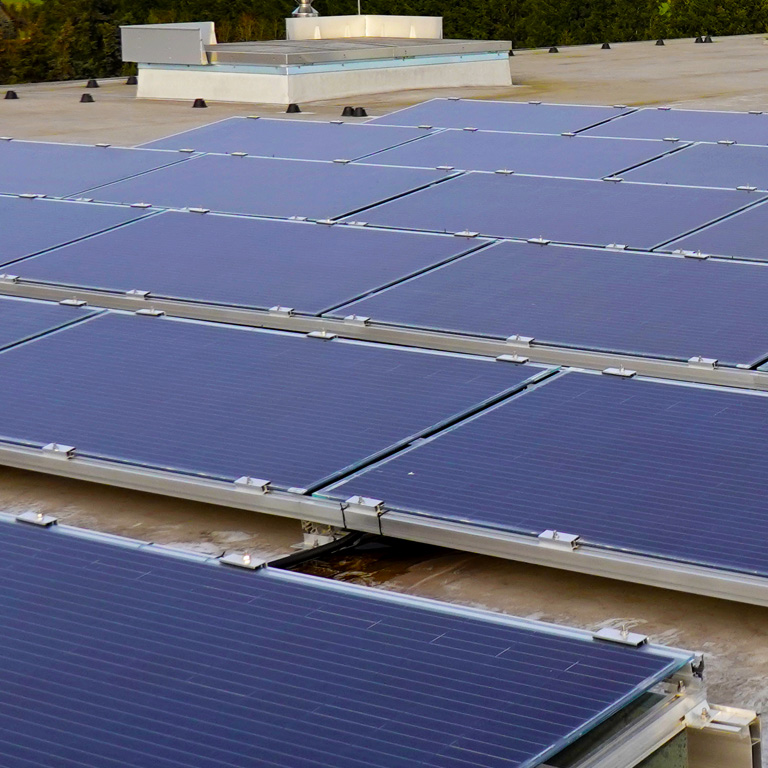
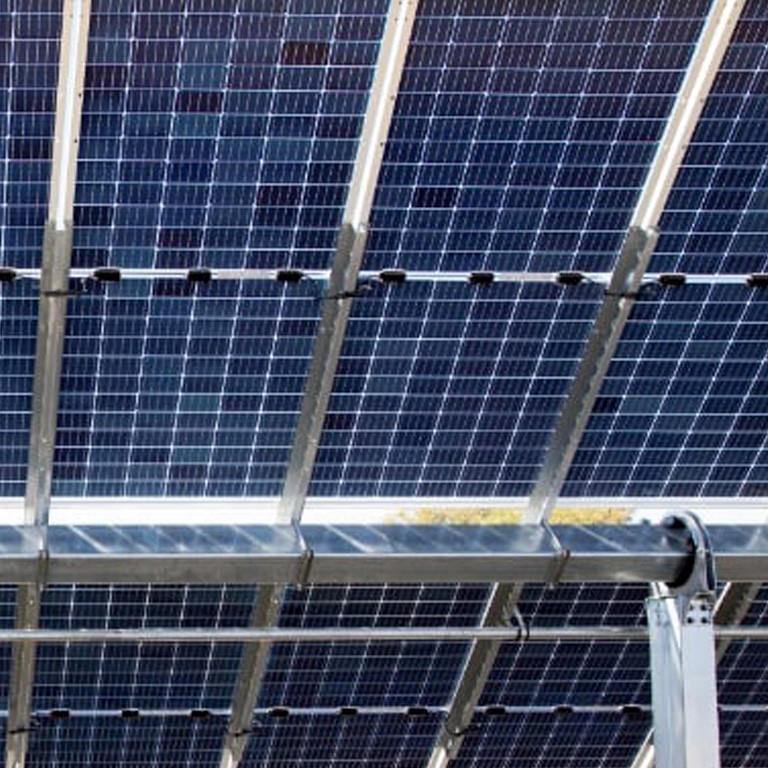